Effects of Impurities in Silicon Nitride Powder on Ceramics
Regarded as the most superior advanced ceramic in overall properties, silicon nitride ceramics feature low density, high hardness, high strength, high toughness, corrosion resistance, and self-lubrication. Its high thermal conductivity (up to 90 W/(m・K)) and near-insulation electrical properties make it highly promising for heat-dissipation and packaging materials in high-speed circuits and high-power devices. Thus, preparing high-performance silicon nitride ceramics has always been a hot research topic in the structural ceramics field. The key to this preparation lies in ensuring the purity and activity of the raw material powders.
This article delves into the main components of the powders used in making high-performance silicon nitride ceramics and the impact of impurities on the final product's properties.
Silicon nitride ceramics are mainly applied in two fields: ceramic balls for bearings and high - thermal - conductivity substrates.
Influence of α - phase Content on Product Properties
With a 4:3 nitrogen - to - silicon atom ratio, silicon nitride is a covalent compound with α, β, and γ phases. The α - and β - phases are the most common. α - Si₃N₄ is the low - temperature stable phase, while β - Si₃N₄ is the high - temperature stable phase. During high - temperature sintering, α - Si₃N₄ transforms into β - Si₃N₄ via a dissolution - precipitation process, forming an interlocked "rod - like crystal" structure. This structure remarkably boosts fracture toughness through crack deflection, fiber pull - out, and bridging. The volume reduction from the α → β phase transformation also compacts the grains, reducing porosity and enhancing mechanical strength.
But higher α - phase content isn't always better. Excess α - phase may cause uneven local shrinkage, harming mechanical properties. In thermal applications, since α - Si₃N₄ has lower thermal conductivity than β - Si₃N₄, residual α - Si₃N₄ after incomplete transformation significantly reduces the ceramic's thermal conductivity. So, adding β - Si₃N₄ rod - shaped seeds to α - Si₃N₄ is necessary to promote phase transformation and ensure thermal conductivity. Currently, the α - phase content in high - performance silicon nitride ceramic powders is usually over 93%, and for high - thermal - conductivity applications, Japan's Ube requires it to exceed 95%.
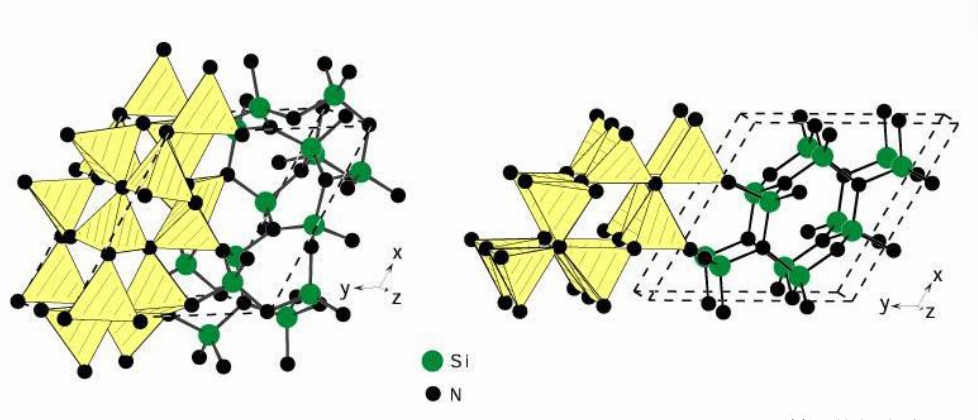
α and β phase silicon nitride crystal structure
Influence of Oxygen Content on Product Properties
Oxygen is a key impurity in silicon nitride powders, adhering to their surface. During sintering, oxygen atoms dissolve into the silicon nitride matrix, creating silicon vacancies and forming lattice oxygen via atomic substitution. Lattice oxygen, a major defect affecting thermal conductivity, distorts the crystal lattice. As phonons (the heat - carrying particles in lattice vibrations) travel through the Si3N4 crystal, they scatter upon encountering lattice oxygen defects. This reduces their mean free path and lowers thermal conductivity. To minimize lattice oxygen and achieve high thermal conductivity, the oxygen content in raw powders must be strictly controlled, typically below 1.5%.

Oxygen atoms undergo solid solution reaction
Influence of Carbon and Silicon Content on Product Properties
Carbon and silicon, with their strong reduction properties, can remove oxygen impurities from ores and regulate the liquid phase's composition and properties when added in appropriate amounts. This promotes the α → β phase transformation and densification rate during silicon nitride sintering. However, when using carbon powder for carbothermal reduction and oxygen removal, the amount must be precisely controlled. Too little carbon provides insufficient liquid - phase regulation, while too much leaves residual SiC, degrading the ceramic's density and electrical properties. In contrast, silicon, when exposed to a nitrogen atmosphere, nitridizes into Si3N4 without generating harmful by - products.
Influence of Metallic Impurities on Product Properties
Fe Impurities: Fe impurities have a dual - edged effect on silicon nitride products. At trace levels (e.g., below 1000ppm), they act as sintering aids. In high - temperature conditions, Fe reacts with the SiO₂ oxide layer on silicon nitride to form a low - melting - point Fe - Si - O - N liquid phase. This accelerates particle rearrangement and grain - boundary diffusion, lowering the sintering temperature and enhancing product density. Yet, excessive Fe impurities (beyond a certain limit) lead to surface blemishes and color inconsistencies, like a grayish - black appearance, affecting product aesthetics. They also introduce free electrons, reducing silicon nitride's insulation and limiting its use in substrates and packaging materials. Moreover, iron ions can raise dielectric loss at high frequencies, impacting applications in microwave communications. For general use, iron content should be under 1000ppm; for high - performance fields like bearings and cutting tools, under 300ppm; and in electronics, where high insulation and low dielectric loss are crucial, below 100ppm.
Al Impurities: Like oxygen, Al³⁺ substitutes Si in the Si₃N₄ lattice, forming the low - thermal - conductivity Sialon phase. This reduces the product's thermal conductivity. High - performance silicon nitride ceramic powders generally require Al impurity levels below 100ppm.
Ca Impurities: During silicon nitride's atmospheric or pressure sintering, calcium impurities react with common sintering aids (like Y₂O₃ and Al₂O₃) to create low - melting - point calcium aluminum silicates. While low - level calcium aids densification, excessive amounts (over 500ppm) result in large glassy - phase clusters. These weaken grain - boundary strength, cause grain - boundary sliding, and drastically reduce high - temperature creep resistance. In addition, the accumulation of calcium ions at the grain boundaries hinders the growth of β-Si₃N₄ columnar crystals and reduces the fracture toughness of the material.